Plastic molding is a great solution for high-quality, long-lasting parts. However, the process is a bit slow compared to 3D printing or CNC machining.
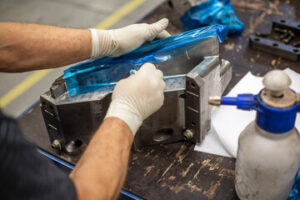
For a faster turnaround time, consider choosing a family injection mold. This method eliminates the need for separate molds and reduces production time. It also cuts down on rework and material waste. Read on American Plastic Molds for more information.
The injection molding method uses heat to melt liquid plastic and compress it into a mold to form a new shape. The molded plastic is then cooled so it maintains its form before it is removed from the mold. This method is commonly used to make plastic replacement parts for metal parts that have become worn or damaged. The process is quick and cost-effective, requiring minimal material waste. The resulting product is strong and durable making it ideal for use in demanding applications.
The key to ensuring quality and consistency during injection molding is maintaining the correct temperature. This is important because it can have a significant impact on the final part’s quality, cycle time, and overall production costs.
Achieving the right melt temperature requires careful adjustment of the injection cylinders and hydraulic system. It also involves adjusting the pressure to ensure that the plastic is packed correctly in the mold. Incorrect packing will result in weak products with low tensile and impact strength. Using a temperature controller with an easy-to-read screen is essential to help you avoid these mistakes.
Another way to improve the injection molding process is to design the mold with uniform wall thickness. This will help the melted plastic to flow more evenly throughout the cavity and reduce the chance of defects such as weld lines and sink marks. Moreover, rounding or tapering thickness transitions will minimize the stress concentration that can be caused by abrupt changes in wall thickness.
Choosing the proper mold temperature is critical for semi-crystalline and thermoplastic materials. Molding these plastics at temperatures close to their crystallization temperature helps to prevent quality degradation and dimensional instability during storage and use. In addition, a consistent mold temperature can help to reduce shrinkage and distortion during cooling.
The plethora of benefits that high-temperature materials offer to the injection molding industry has been well documented. They are a catalyst for innovation, opening up avenues of design flexibility and engineering marvels that would not be possible with other materials. Their resilient nature and adaptability also enable them to flourish in a challenging environment of increasing demands.
Low-Temperature Method
Injection molding is one of the most common methods of producing plastic parts. It involves injecting liquid plastic into a mould, where it is compressed together to form the desired shape before cooling and being removed from the mould. This process requires precise temperature control to ensure high-quality, consistent products.
The injection molding process is used for a wide variety of products, from small components to entire body panels. It is a versatile and economical method for making replacement parts for many products that have worn out or broken. The moulds are made of metal, usually steel or aluminium, and are precision-machined to match the design of the product. The finished plastic part is then ejected from the mold using a system of pins, sleeves, or strippers.
In order to produce high-quality plastic parts, it is important that the mold temperature is consistent. Incorrect temperatures can cause the product to have varying shrinkage rates, which can result in warping and deformation. The proper temperature is determined by the material properties, performance requirements of the product, and the mold size.
Using the low-temperature method of molding allows plastic to cool at a lower rate, which reduces internal stress in the molded part. Internal stresses are caused by different thermal shrinkage rates in the different areas of the plastic during cooling. This results in a buildup of pressure and tension that can lead to cracks in the plastic. A higher mold temperature helps to reduce the internal stresses in the molded part by slowing down the cooling process and allowing the plastic to shrink evenly throughout the product.
Low mold temperatures can also create obvious weld lines in the finished product, which reduces the strength of the plastic part. For crystalline plastics, a low temperature can increase the crystallinity and lead to a greater tendency to stress cracking. Using a moderate mold temperature can reduce these problems by raising the plastic’s temperature to a level that is appropriate for its viscosity and other processing conditions. Raising the mold temperature can also reduce the tendency of amorphous plastic materials to develop internal stress, which can be seen as obvious stress marks on the surface of the finished product.
Continuous Moulding Method
In the continuous casting method of plastic molding, a hot metal is cast into a mold of indeterminate length. This allows the molten metal to keep moving downward, even as it solidifies into the casting. This eliminates slag, which can lower product quality, and reduces the need for extensive machining or rework.
The continuous casting method can be used with many different types of plastic materials, including metals like copper and zinc. It also produces higher-quality products than other casting methods. The improved microstructure of the finished metal reduces defects such as segregation and porosity, which can lead to lower mechanical properties.
This process can be used to produce a wide variety of products, including tubes, rods and wires, as well as profiles for building applications and medical devices. It is especially effective when the product requires a long, consistent cross-section. It can also be used to create complex shapes.
The extrusion method involves using an extruder to shape a raw material, usually a thermoplastic, into the desired shape. The plastic is then cooled to its solid state and cut to the required length. The advantages of this process are that it is cost-effective and suitable for high production volumes. It also offers a high degree of flexibility when it comes to designing the product’s profile.
It can be used to produce a wide range of different products, from syringes and pipettes to industrial components, such as valves and actuators. It is also an efficient method for producing long, hollow formed products.
Rotational molding has a long history beginning in the 1800’s when rotation and heat were used to produce metal artillery shells. Today, it is one of the most economical plastic molding processes. It allows for a variety of design options and can be used to produce hollow plastic parts. The mold is able to include curves and contours as well as slots for metal or plastic inserts. This helps to provide the strength and durability needed for a variety of products, such as kayaks, bulk containers and storage tanks.
It is important to choose the right plastic mold for your project. The experts at Plastek Group can help you understand the benefits of each type of plastic molding. We can also help you decide which process will best suit your needs and budget.
Extrusion Method
This technique involves pushing a liquid plastic through a shaped die to create long linear products like hoses, pipes, drinking straws, and curtain rods. It is a high-volume manufacturing process that works well for producing durable, weatherproof products and parts that have a consistent cross section. It is also used to produce shapes that can’t be achieved with injection molding. The raw material is heated to a high temperature before being forced through the die, which is designed to shape the final product. Once the molten plastic has been pulled away from the die, it is cooled to set into its final form.
The extrusion method is a good choice for making complex shapes because it allows for much greater design flexibility than other methods. This is especially important for medical applications, where precision and accuracy are paramount. However, it is important to note that it is not suitable for all types of plastics. It is important to pick the right plastic for each application, as different materials have unique properties that affect how they perform in a given environment. For example, polyvinyl chloride (PVC) is a good option for products that need to resist harsh chemicals, while acrylonitrile butadiene styrene (ABS) is ideal for products that need to withstand heat and radiation.
After the extruded product has been cooled, it must be stretched and rolled to ensure that it holds its new shape. This step can be done in a number of ways, depending on the product. For example, blown film extrusion uses cooling rollers and air to cool the molten plastic. For pipes and tubes, a sealed water bath is typically used.
The forming of plastic extrusions is a complex process that requires a lot of skill. A skilled team can make products that are extremely precise and high-quality, but it’s important to keep in mind that it isn’t always possible to get the exact shape you want with this method. This could be due to the cooling rate, how much the die swells, or other factors. For this reason, it’s often preferable to use injection molding or 3D printing for more precise designs.